"I've put out a few fires!"
FIRE SAFETY TRAINING
"I've put out a few fires!"
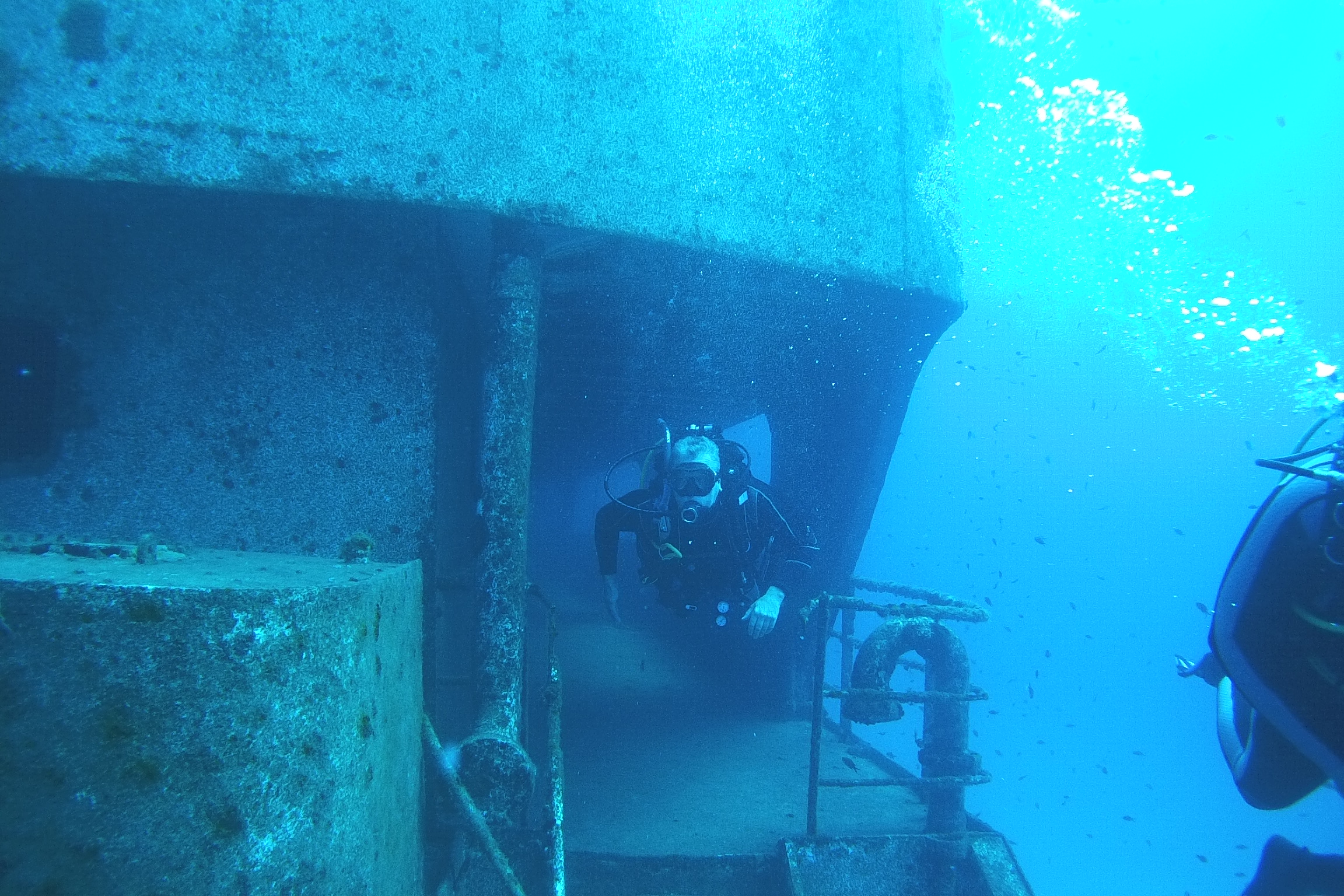
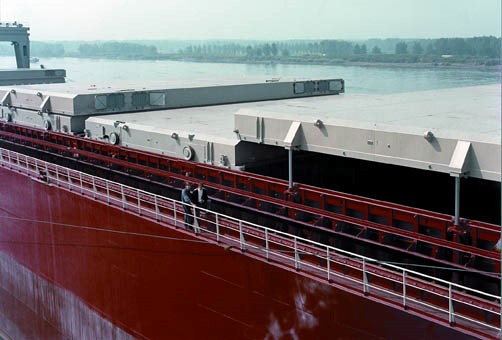
ETD Training MD, Phil Gutteridge, reveals how his experiences as a ship’s safety officer shaped his role as an employer - and are relevant to any workplace health and safety training.
Although most people don't work in a maritime environment, there is much about the way that a well-organised ship is run that can feed directly to improvements in land-based workplace health and safety. Consider for a moment the nature of the environment that a ship is required to operate in. Initially, there is the sea.
Yes it can look beautiful and serene. 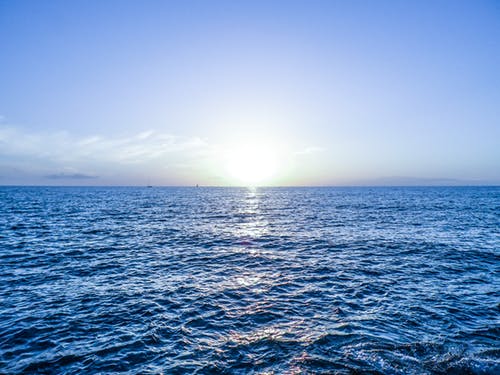
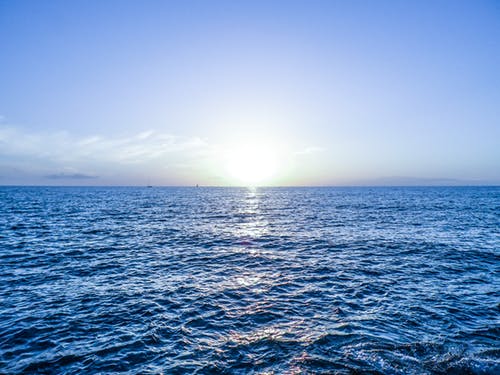
Yes it can hold our interest with its indigenous life forms when they show themselves.
Yes, it can supply an abundance of food stuffs from within.
Yes it can provide us with two of human life’s most needed commodities - water (if we treat it so that we get just that - water) and salt.
However, any more than a cursory look and we quickly deduce that it is not an environment that is overly considerate of our wellbeing. In fact, it is not gifted with thought or reasoning processes at all and as such, it is oblivious of sentiments such as compassion or reason. This is hardly surprising: Its power source is ultimately the Sun - so what do we expect; a smiley face?
The sea can be a very violent place -for days on end. In seconds, a human being on a ship can be moved well over forty feet in three dimensions. Further a person’s angle (usually perpendicular to the horizontal when standing) can change by 60 degrees as they move those forty plus feet in multiple directions. Not what you would call a stable environment ordinarily. Some might reasonably add that the environment inside, outside and certainly off the ship is, by definition, a health and safety risk. That’s before we start to consider other vessels in the near vicinity, subsurface hazards such as rocks and banks or buoys. There are other added complexities, but I won’t bore you because we have all this before anything actually goes wrong with either the ship, or anyone or thing on board.
At one time, I navigated ocean going ships, which meant that I was also responsible to ensure that when in port - and the navigation element wasn’t needed - they operated safely and successfully; loaded and/or discharged their cargo with maximum efficiency and safety. Within this, I quickly came to realise that there were some variables that were under my direct control and some that I had no control over at all. If something under the latter category occurred, how myself and my team reacted would decide whether we had a good day or a bad one.
There is no substitute for experience. It’s an old cliche but it’s true, and especially true when that experience is supplemented with essential knowledge and acted upon. You can become hardened and acclimatised to having to think in certain ways. It is on the basis of this knowledge experience mix that many of the health and safety measures on ships are evidenced as Standard Operating Procedures (SOP).
Essentially an SOP is simply a methodology used for a given purpose, or to deliver a given end result appropriate to any given task or objective in a given environment. There are undoubtedly other definitions but that should suffice for now.
So, in this regard we have SOPs in port, SOPs at sea, SOPs when a collision situation exists, SOPs in cases of injury or medical emergency, SOPs for firefighting - and even SOPs in case all else fails and we have to part company with our temporary home under less than ideal circumstances.
What has this to do with our office, our factory, our truck, our cutting device, our tree climbing equipment? Nothing, or very little in practice, but a surprising amount in principle. SOPs should also extend to training, maintenance and testing. Allow me to draw some simple parallels.
Fire extinguishers are pretty much the same in most parts of the world. Do you have a qualified person who can refill them if they are used? If you do, then fire drills can be slightly more exciting and useful because you can discharge one and give people the chance to experience what it is like to use one. If not, then your fire equipment testing organisation might well be happy to stage some safe mock ups for using the extinguishers when they make their annual pilgrimage to inspect your equipment. This might well make fire drills a bit more - fun.
We had fire drills weekly when at sea and every officer had a minimum of five days training in fighting shipboard fires - from small affairs in accommodation to major cargo or engine room fires. The fire teams that trained us made them as realistic as they could in terms of heat intensity, smoke, cramped and difficult to reach. That gave us the knowledge bit. When I came to experience the fires for real, they held no mystique but I did respect them and knew what measures to take to break the fire triangle on a much larger scale.
Are you prepared for fires - or is it a case of the occasional alarm going off and everyone sauntering gently through the nearest escape door? What about the possibility of noxious smoke fumes? Do you have any idea of just how quickly even a large space can fill with smoke - noxious or otherwise? It doesn’t help breathing and no breath equals diminished energy, poor decision making and ultimately death. In fact, fires kill far more people by smoke than ever by flame - although a closed room can very quickly become a suffocating prison as the flames quickly use up all the oxygen.
Do your staff know where each extinguisher is and what fires they can be used on? Don’t use a water extinguisher on an electrical fire or near electrical equipment! You probably knew that, but just in case.
Are there any operations that might present a slightly higher risk of fire than normal routine operations? Is it worth having up to date spare extinguishers that you can pull out and locate near the areas of increased risk when that operation increases the risk?
What about cutting equipment or presses? How often do you check emergency stop systems? Do the operators all know what it feels like to hit that red button? We check ours at least twice a day from different positions. It takes seconds to activate and reset and at least you can be as certain as possible that if you ever have to do it for real, it is as probable as you can be sure of that it will work. Keep records if you don’t already. Prove you are safety minded.
Everything we did in that fairly dangerous environment was covered, as far as we could make it, by an SOP based on knowledge and experience. Very few ships sink but lifeboats were tested: Their rations were checked very frequently; water was kept fresh. Moving parts were kept oiled or greased against the ravaging effects of salt water and spray. Plugs to the boats were inspected to make sure they sealed and were not going to disintegrate. The boats were swung out to at least embarkation level. People were tested. Communications were tested. Systems were tested.
The Royal Navy make it even harder. They do it (fire) with real smoke while simulating a full scale sea battle and then further simulate a man overboard in the middle of it with a medical emergency or two thrown in for good measure! The thing is, it’s realistic and makes people as ready as they can be in case it ever happens. You don’t necessarily have to go to these lengths - but you can see how an ex-Navy person might be slightly amused by the bi-annual trot through the door to a muster point that could just be right in the smoke line in reality. Not good if the smoke from the burning building is noxious!
Much of our firefighting equipment was deployed before we arrived in many ports (where we were sure that it wouldn’t be stolen and sold by impoverished or criminally minded locals). That meant it was ready to go if needed which, in turn meant valuable minutes and seconds saved.
What about first aid kits? Are these standard off-the-shelf kits or do you weight them with supplements more likely to be useful in the environment in which they are placed? For example, if the risk assessment around a given piece of machinery is that a cut is more likely than an impact injury, do you load up with extra dressings, plasters and cleaning/sterilising stores?
We could go on ad infinitum but the important thing is to give some serious thought to your environment and to have an equally good look around and do your level best to identify ahead of time what could go wrong, what training is needed to cope with those things and how can maintenance and testing prevent things from going wrong and enable people to cope if it does?
Do you test your fire escapes weekly? Are your escape signs and routes clearly marked or have they been damaged? Can people get out even if they can’t see (smoke)? This is a dickie one to test but just thinking about it can help decide policy and identify training needs and make you better prepared.
One thing we can pretty much guarantee: The very thing that you prepare for probably won’t happen, but if your SOPs are robust enough in principle and tested enough in practice environments, then if a variant of what you prepare for should ever happen, you and your team will be much better placed to think about the variations than be taken totally by surprise and wrong-footed.
Check and test everything against its environment and the people who will need to use it and do it far more regularly than statute requires. If you know everything is ready, you and your team are more likely to be ready too.